Dean DeBiase is a best-selling author and Forbes Contributor reporting on how global leaders and CEOs are rebooting everything from growth, innovation, and technology to talent, culture, competitiveness, and governance across industries and societies.
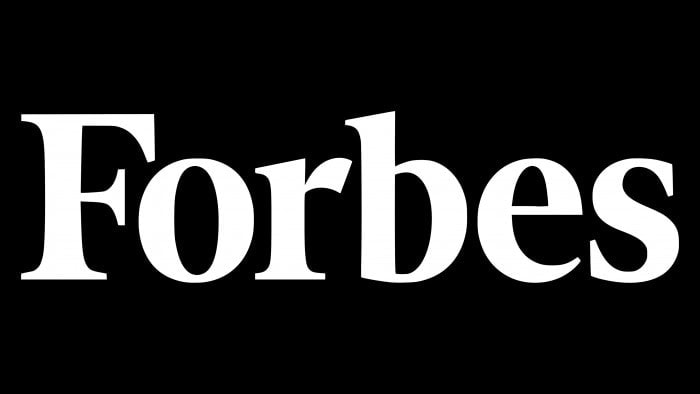
American Policy To Drive Revival Of Technology And Business Growth
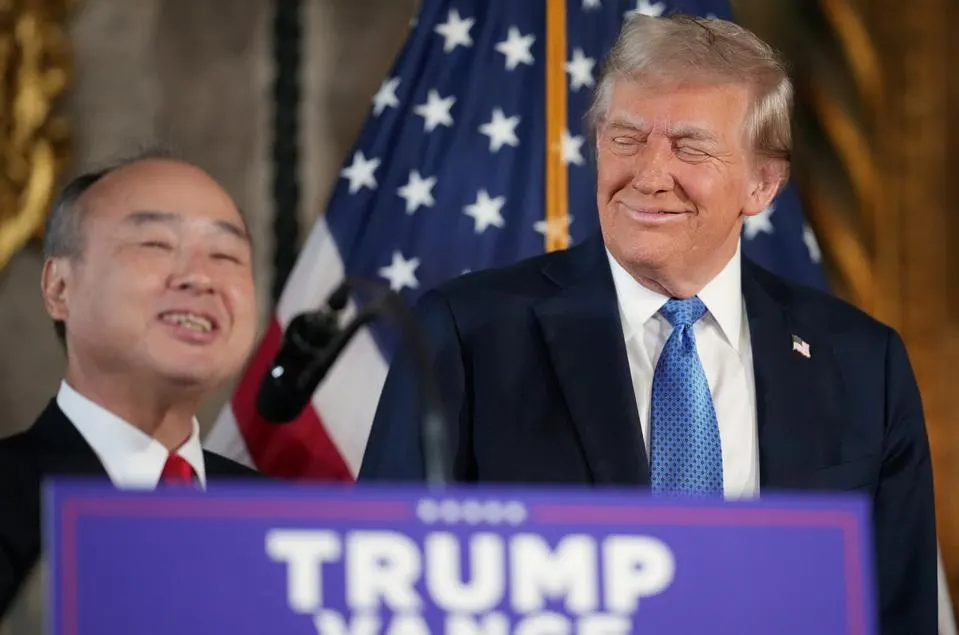
By Dean DeBiase
December 16th, 2024
While I was testing out Grok, Elon Musk’s xAI chatbot, with advancements that seem to hinge on inexhaustible power and data demands—President-elect Donald Trump and SoftBank Group (ADR) CEO Masayoshi Son announced a $100B investment into U.S.-based artificial intelligence and enabling AI infrastructure like data centers, chips, and energy.
With more CEOs committing to U.S. growth and innovation investments, my thoughts jumped to how this will impact America’s economic revival, and accelerate two of our challenges—quantum computing and electric power. These two areas will eventually reboot most sectors, including AI, high-performance computing, and the power-hungry computers that make it all happen.
The U.S. Policy And Investment Surge
Here in Illinois, we have been working on becoming an American quantum computing hub, e.g. building the Illinois Quantum and Microelectronics Park (IQMP), in the vacant U.S. Steel site on Chicago’s lakefront. Once finished, this massive campus will house a perfect (network) storm of co-located corporations, startups, national laboratories, federal research offices, and universities.
Launching the next-generation of computing, at the epicenter of what was once the largest steel manufacturing site in the world, is not just a bold move—it’s symbolic—as the technology can also help fuel the revival of American manufacturing. More on that in a bit.
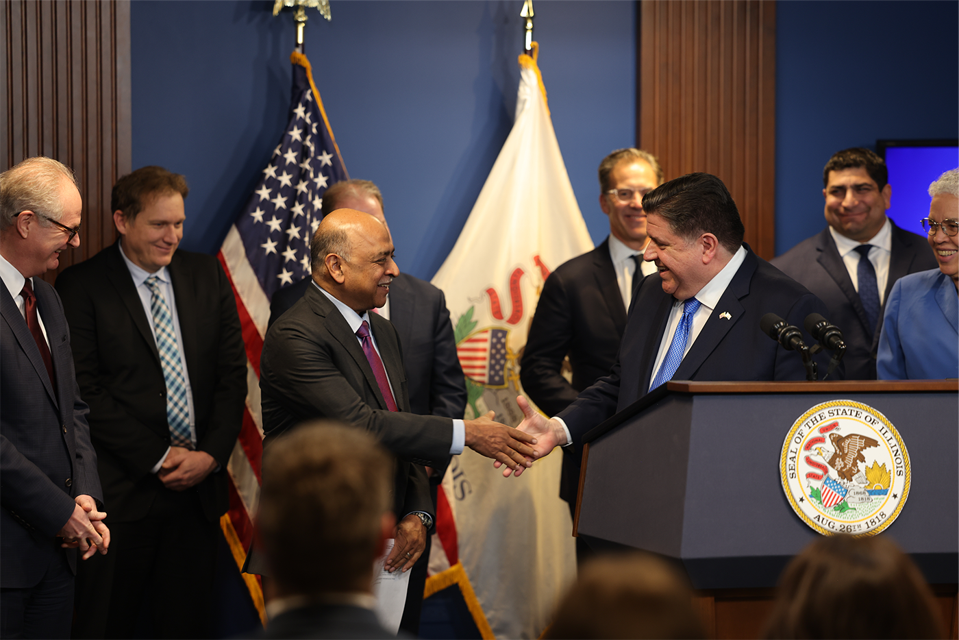
Illinois Governor J.B. Pritzker has been leading the charge securing billions of investments in the state—and recruiting partner companies, like PsiQuantum Corp and IBM (IBM). Announcing it will be the first Fortune 500 and a founding partner of the National Quantum Algorithm Center in Chicago, IBM Chairman and CEO, Arvind Krishna stated, “This new partnership with the State of Illinois and its thriving innovation ecosystem brings us one step closer to defining the future of computing. With IBM’s best performing quantum hardware and software in the heart of Illinois’ innovation network, together we can truly unlock the potential of quantum computing to solve the world’s hardest problems.”
Speaking of our hardest problems: Facebook (META) just announced it is investing $10B in a single “hyperscaler” data center in Louisiana for its massive AI processing needs. Think artificial super intelligence. But, what about the power needed to drive data center GPUs? Both Microsoft and META are exploring nuclear energy to power these kinds of data centers. About time—smart move.
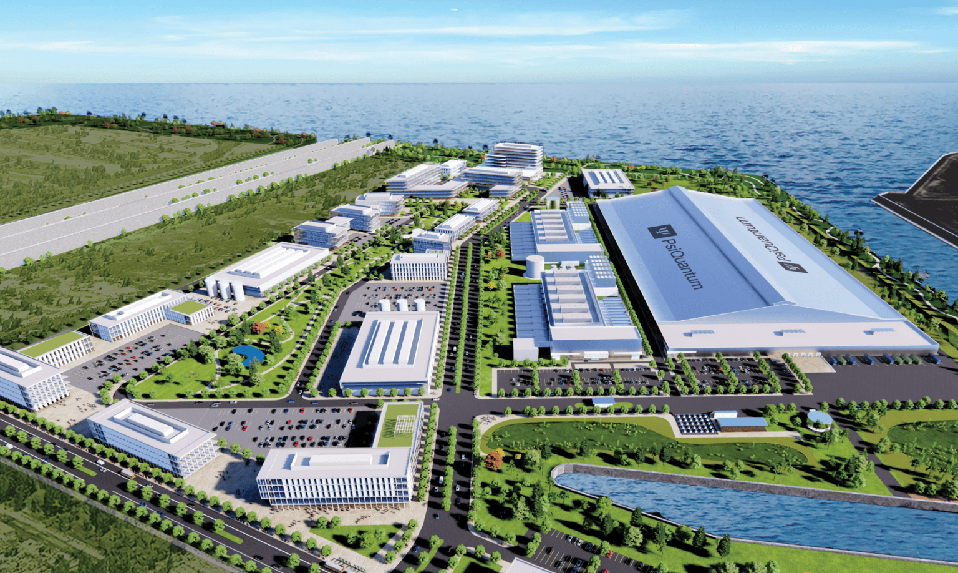
Softbank has no doubt noticed that China is targeting Nvidia, the chip vendor that’s been in the catbird seat, as its processors are the horse to beat (sorry to mix metaphors) when it comes to training data-hungry LLM models.Nvidia is the big dog in the data center GPU space, with an estimated 88% market share—and some think quantum company IonQ (IONQ) could be the next Nvidia. But, for now, the OpenAI plus Nvidia duopoly (or OpenVidia, as some call it) is driving a trend towards data centers that are purpose-built to handle today’s AI needs while paving the way to an eventual artificial general intelligence (AGI) Mecca (or singularity, whichever comes first). It’s a big tent with room for many global players.
Discussing these advanced tech trends with a group of manufacturing CEOs and government officials in Washington DC, I began to rethink—where is this all going? And before the next level of energy sources and quantum capabilities arrive, isn’t there a better, more energy-efficient way to scale and derive AI benefits now?
Never leaving serendipity to chance, I happened on a small, little-known company with an MIT pedigree that may help produce results without users breaking energy or data banks. I’ll get to them shortly. But for context, let’s take an historical tour of an area they serve—manufacturing. I like this sector because its revitalization holds the key to driving American global competitiveness, even before quantum arrives.
From Robots To Machine Learning
AI got its start in manufacturing even before it was the AI we recognize today. One of the first industrial robots, Unimate – in the ‘60s, automated manufacturing operations that were too dangerous, difficult, or otherwise challenging for humans. These machines were programmable but lacked advanced decision-making capabilities.
Real AI only became a factor in subsequent industrial robots. E.g. in 1968, neural networking pioneer Marvin Minsky developed the Tentacle Arm, a computer-driven and hydraulics- powered robot, at the MIT AI Lab.
In the 70s, AI moved beyond robotics automation to provide the smarts in computer-assisted design (CAD) software and computer numerical control (CNC) machines. In the 80s and 90s, it made its way into computerized maintenance management systems (CMMS) and manufacturing execution systems (MES).
The introduction of machine learning during the 90s and 2000s vastly improved AI, boosting efficiency and lowering costs.
I Can See Clearly Now
AI-powered machine vision began to enter mainstream in the 2000s. These systems tap powerful computing and video cameras to assist robots, recognize patterns and detect quality flaws in components. Companies like Cognex and Keyence became leaders in deploying machine vision for automated quality control.
The real boom in AI-powered machine vision came with the rise of Industry 4.0(i.e., the so-called fourth industrial revolution, or the integration of digital technologies into manufacturing and industrial processes) in the 2010s, as manufacturers sought to integrate real-time data analysis and intelligent automation. AI enhancements allowed machine vision to detect anomalies and monitor product quality
While machine vision excels at specific tasks like parts inspection and defects detection, these systems are not designed to provide holistic insights into manufacturing processes, especially where frontline workers play a big role, e.g. for complex products or production runs. Moreover, machine vision was designed to analyze still images, not video.
Circa 2020, manufacturers could try to get a holistic view of operations via sophisticated AI systems and IIoT sensor data. Still missing was the ability to employ video analytics that could “see” and “understand” the actual work being done by machines and humans on production lines.
Seeing The Forest And Trees (Assembly Line 2.0)
That is why I was intrigued about the work Leela AI is doing. Their team gained instant credibility when I heard of the connection with Marvin Minsky, a cofounder of MIT’s AI laboratory, and widely regarded as a father of AI. In particular, Dr. Minsky was a pioneer in neural networking— an important element of their platform. The firm is an outgrowth of the three co-founders‘ research at MIT and Marvin’s son, the firm’s CTO Henry Minsky (sadly, Marvin passed away in 2016).
Leela’s hybrid AI model combines methods in cognitive intelligence and neural networks to learn as an infant does. When applied to vision systems, it can “see” everything happening on the shop floor, and better “understand” what’s being seen.
I spoke with Leela AI CEO Cyrus Shaoul, who explained: “Before, manufacturers could only guess at what the people were doing in between the machines, short of old school, manual time and motion studies, to track each assembly process and unveil waste reduction opportunities. Our holistic visual intelligence can analyze every shift on every line, spanning lines, to measure activities with accuracy and granularity never before possible. The technology not only eliminates bottlenecks but also protects worker safety, aids training, and improves quality.”
Through more digging I learned that Leela AI was not the first to apply video analytics to manufacturing. Drishti was. They were acquired by Apple, and others have since entered the market.
When asked about what sets Leela apart, Dr. Shaoul explained that it gets down to AI that offers faster training and deeper insights into video. He said: “It springs from LAMs (Large Activity Models). When you multiply the number of things people can do with the quantity of things in the environment, you get a very large number of possible actions. The core IP inside Leela enables it to recognize a much larger number of activities than other models and is more accurate than the multimodal models like OpenAI.”
American HMLV Manufacturing Revival
This capability is important because it could be decades before robots can more affordably and accurately accomplish most of what human frontline workers can do, especially in the US, where there’s a lot of high mix, low volume (HMLV) manufacturing with much variation and manual steps involved. In the fight for an American manufacturing revival, HMLV will be a key competitiveness tool, and AI needs to help here soon.
I asked Cyrus to provide hard numbers and examples. He explained: “We deliver a 50% reduction in safety incidents. Customers typically see a boost of 10% to their production capacity. So that’s a lot of business value, if you can see what’s happening and if an AI can help better understand what’s being seen and then take actions based on that.”
Another advantage of this kind of AI is that it may not require massive amounts of data to train the models or lengthy training and inference cycles. Leela has found a way to do advanced machine vision while consuming 100x less energy in both training and inference.
Drew Satorius, Global Director of Advanced Manufacturing Technology at BAC, was looking for a way to get real-time production activity data from the assembly area. He brought in Leela to get the data that would help reduce waste by making data-driven decisions to improve their processes.
Leela records assembly cycle time for each station, as well as value vs. non/value added time. It tracks tool and equipment use and measures tasks such as picking up, carrying, and using a variety of tools. This helps them compare metrics between stations, shifts, and time periods.
Satorius noted that “Leela’s solution has helped us gain a deeper understanding of bottlenecks with insight into operational improvement opportunities. We can now focus more of our time and energy on making progress instead of collecting data. We can mobilize teams to make improvements quickly and, due to the real-time continuous analysis, we can quickly see the results of our AI-augmented decisions.” Sounds like impact.
The Business Revolution Will Be Televised
As I watched Donald Trump and Masayoshi Son on CNBC, kicking off what many C-suite leaders think will be the next business revolution, I reflected on how far tech has come. But when you tour most factories, you won’t see enough of it yet. It needs to become more systemic and efficient. As smart manufacturing matures, visual intelligence will be critical in self-optimizing factories, where AI makes continuous improvements.
Time to get ready. As American growth policy and investment surges in the second half of this decade, and billions are invested into the next generation of enabling technologies, look for transformational opportunities across industries—not just manufacturing—including the sector you’re in now, or you may be in soon.